Home > General Chat > TIG Welding experiences.
|
TurboDave16V
Forum Mod
10980 Posts
Member #: 17
***16***
SouthPark, Colorado
|
|
Hey you guys!
Figured I'd share a few thoughts and also get feedback from you guys on other stuff you've learnt or experienced as lots of us have learnt the hard way through trial and error!
So, I've been struggling with my welding of late and figured I'd share some stuff.
Welder: Miller 210Dx with air-cooled torch and pedal control. Almost always reach for 2% lanthanted tungsten as it's good for welding everything - I don't even re-grind after welding different materials or process (DC > AC for example).
Several reasons why things went off the rails are listed below.
1) I didn't realise that my eyesight was disappearing on me. I already had the weakest "cheater lenses" in my miller welding helmet, but have now bumped to a 2.0 lens. Night and day difference.
2) I just couldn't get a consistent focus on the arc in AC mode when doing ally. I grind my tungsten's on a bench grinder, using the left wheel to rough the shape the "wrong way" (circumferentially) as its a lot quicker, then switch to the right wheel to grind axially to finish - always making sure that I remove the material leaving none of the previous grind. Incindetally, I cut comtaminated tungstens with a disc cutter, so as not to contaminate the wheel.
I've been blaming tungstens, gas, everything. The inconsistency is what really annoyed me.
I then purchased one of those hand-held tungsten grinders (that look like an overpriced dremmel) and suddenly I have a perfect, focused arc... What the fudge has happened? I follow the same process of my grinding routine, but add this last stage, and its night-and-day consistent from grind to grind. I even re-faced my "finishing" wheel, but it's simply not as good as I believe it used to be. Contamination perhaps? Or maybe it's just rougher as its reduced in dia (unlikely) or have I personally got better and more critical over time?
I've seen some folks using belt sanders, or even a smooth flap-wheel on the angle grinder. What do you use? After experimenting, I'm sure that Arc scatter caused by "correct technique, but poor results" has been hindering my alloy tig skills for a long time.
3) Next thing I realized is that the arc would appear "hazy".
Not blurred, but hazy... This of course made detailed welds a challenge. This I figured out last night. The lighting above where I sit at my bench, depending on if I'm looking forwards or more looking down, was glaring into my helmet and adding just enough light inside my helmet to cause this effect. Another inconsistency that took me forever to figure out - VERY frustrating again. Not too sure how to address this - maybe adding some of those "diffuser lenses" (like in offices) over the lighting around the welding table, but I fixed it immediately for now by throwing a hat on while welding lol...
4) Tungsten.
Having been using 2% lanthanated for everything, I switched to pure tungsten as part of my experimentation (when I had wrongly convinced myself that the tungsten was at fault) and realized that maybe this is the best tungsten for certain alloy welds given its characteristics to ball the tip. Welds like outside corner joints on long, consistent straight runs straight runs for example (like intercooler end tanks).
I need to do more practicing on this - what are your experiences?
Cheers, and I hope everyone is doing good in these weird times!
Edited by TurboDave16V on 16th Oct, 2020.
On 17th Nov, 2014 Tom Fenton said: Sorry to say My Herpes are no better
Ready to feel Ancient ??? This is 26 years old as of 2022 https://youtu.be/YQQokcoOzeY
|
Joe C
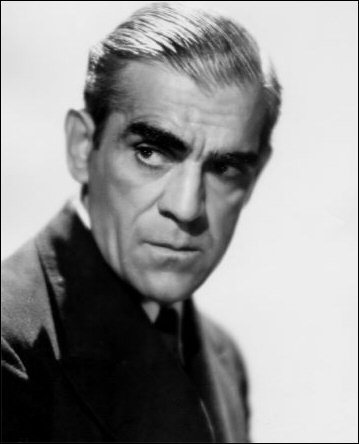
12307 Posts
Member #: 565
Carlos Fandango
Burnham-on-Crouch, Essex
|
|
Ive found tungsten finish can have a big effect, i tend to "polish" them with a belt sander, ie a tickle after grinding to knock any rough finish down turning them very slowly so any marks ar longitudinal rather than spiral, also a wipe with alcohol or similar is worth while,
tungsten diameter can be a major factor, after trying to weld stainles tube with a fat tungsten ( becase I couldnt be arsed to change it) swaping to a 1.6 was like a miracle. now I always use 1.6 for stainless ( unless its a big lump) and go straight for 2.4 or 3.2 if its thicker for ally.
Tungstens material I have faffed with, but cant remember the results, but I think it was basically go with the miller recomended material
Gas I have had a bottle that gave weird results, bottle run out, and woth a new botlle and changing nothing else everything sudently worked much better.
I doubt it makes a difference, but I dont normally cut tungstens, I tend to snap them off, quality tungstens should snap pretty clean and cheap shite ones... whats the word, delaminate?
On 28th Aug, 2011 Kean said: At the risk of being sigged...
Joe, do you have a photo of your tool?
http://www.turbominis.co.uk/forums/index.p...9064&lastpost=1
https://joe1977.imgbb.com/
|
stevieturbo
3594 Posts
Member #: 655
Post Whore
Northern Ireland
|
|
There are quite a few videos on youtube, where guys have used different tungstens, different grinders, different cleaning etc etc...and I guess yes, each one does all make a difference. But where they all huge ? not really.
I will say I'm not a good welder....but I grind mine with a flap wheel, trying to grind towards the top.
I think I'm currently on blue tungsten, would need to check.....I almost always use 2.4mm. 1.6mm just way too thin and melts easily.
I used gold before that...although really couldn't say one way or the other which is better.
But yes arc focus can be difficult, setting frequency as high as it will go seems to help this.
ALthough I also learnt recently that part of my tungsten melting issues, were due to the "cleaning" setting or percentage. Called different things with some machines. I usually had it around 50%, but moving it more towards the material end, means less time burning away at the tungsten, so less melting when welding say an intercooler that needs a lot of current to get it going.
But for the most part, on sensibly thick material...ie 2mm upwards is a doddle. 1.6mm....still ok but need to be a little more careful.
But I can do decent welds without too much difficulty.
I also always use 2.4mm filler...I always melt the crap out of anything thinner before it's anywhere near the weld lol.
I did also recently get one of those FUPA #8 clear cup things...I think it does help a little, and although I haven't tried much, seemingly it also allows a lot more stick out if that may help in tight areas.
Should probable also add..the change to Furick was from a cheapy gas lens...so not the regular stuff that comes with a torch ( I think....had the stuff for years so not sure what it originally came with )
Edited by stevieturbo on 16th Oct, 2020.
9.85 @ 145mph
202mph standing mile
speed didn't kill me, but taxation probably will
|
stevieturbo
3594 Posts
Member #: 655
Post Whore
Northern Ireland
|
|
https://www.youtube.com/watch?v=ZI3SyGjjbfw
https://www.youtube.com/watch?v=EfKjIZijsP0
https://www.youtube.com/watch?v=mdz2vrQ5m8c
https://www.youtube.com/watch?v=HqGK13SVHOc
Kinda makes me wonder why grind for alloy ?
https://www.youtube.com/watch?v=dVbnWfw6QJw
US colours are different than UK though
https://www.youtube.com/watch?v=DzEuV83UGMY
9.85 @ 145mph
202mph standing mile
speed didn't kill me, but taxation probably will
|
DILLIGAF
174 Posts
Member #: 9128
Advanced Member
|
|
Pure Tungsten and Inverters don't really work well together, not sure why but they don't.
Zirconiated is the equivalent for a Inverter and Alloy, I was using Lanthanated coz they do both as well. But after someone suggested the Zirconiated and after trying them I won't be going back to one tungsten for everything.
|
Tom Fenton
Site Admin
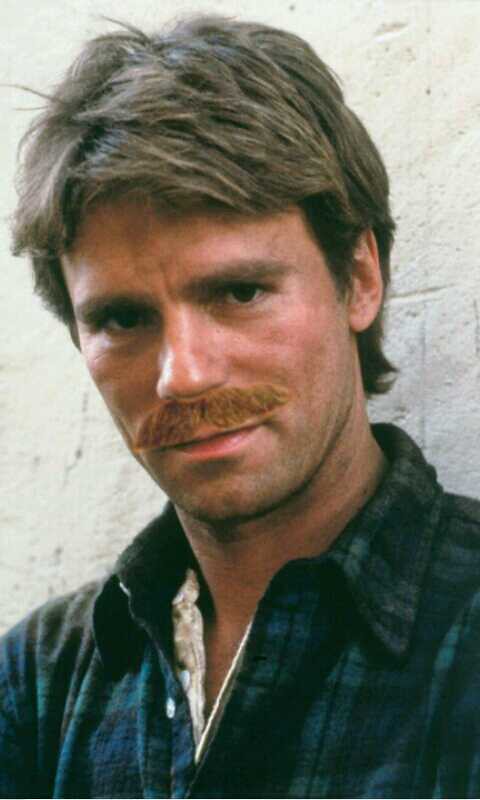
15300 Posts
Member #: 337
Fearless Tom Fenton, Avon Park 2007 & 2008 class D winner & TM legend.
Rotherham South Yorkshire
|
|
I’ve always used red tip for ferrous and grey tip for ally. Just what I was told by a pal of mine who is a better tig welder than I’ll ever be. Cleanliness is the biggest thing I’ve found, especially on alloy using any kind of abrasive to prep the surface just leads to a black horrid mess when you show it the torch.
On 29th Nov, 2016 madmk1 said:
On 28th Nov, 2016 Rob Gavin said: I refuse to pay for anything else
Like fuel 😂😂
|
shane

2643 Posts
Member #: 1246
Post Whore
Lowestoft, Suffolk.
|
|
Usually use thoriated or lanthanated for steels and zirconiated for ally.
Tunstens ground on a bench grinder, I have noted issues with arc stability in the past but after reading this thread I may experiment next time I break the welder out.
Agree with Tom on the cleanliness / abraded with scotch bright then wiped with acetone.
Shane
|
stevieturbo
3594 Posts
Member #: 655
Post Whore
Northern Ireland
|
|
For cleaning...I usually just wipe with stainless brush or wire wool. If the metal is fairly new etc....I've never really had any issue.
Don't think I've ever tried using acetone.
But I certainly wouldnt try to weld anything dirty if it could be avoided, or if for some reason it cannot be ground or burred clean...you may need to try and burn it clean with the torch, prior to actually getting a welding puddle started, but that tends to be messy.
9.85 @ 145mph
202mph standing mile
speed didn't kill me, but taxation probably will
|
Home > General Chat > TIG Welding experiences.
|
Users viewing this thread:
none. (+ 1 Guests)
|
|
|